Two recent experiences come to mind. The first occurred during a meeting I had in a newly renovated Class-A commercial property in midtown NYC. The lobby was stunning; the concierge desk was sleek and professionally outfitted. But when I stopped in the restroom, it looked as if it hadn’t been serviced in weeks. I tried three different soap dispensers just to get enough product to adequately wash my hands.
We’ve all seen it before, and perhaps way too often: the ill-serviced public bathroom.
It wasn’t much different later on when passing through a major airport in California. Things looked generally disarrayed, wastebaskets overfilled, a few stalls were understocked. Of course, as with most public bathrooms, both of these facilities were equipped with the all-too-familiar inspection checklist that hung near the row of hand dryers.
In both cases, as if to accurately represent the state of the bathrooms themselves, the paper checklists rested in dilapidated plastic sleeves that were scotch-taped to the wall.
A few quick observations regarding the data collected on these checklists. The self-reported timestamps were probably unreliable. In one case, the inspection OUT time was two minutes prior to the IN time (here’s to Michael J Fox in Back to the Future). Work spent in the bathrooms usually varied from 5 to 16 minutes. This is not a lot of time, so what did they do or replenish? In some instances, inspection times took much longer to complete. Why or what was done differently?
In short, none of the documented information was particularly insightful, and probably safe to say not particularly useful to management.
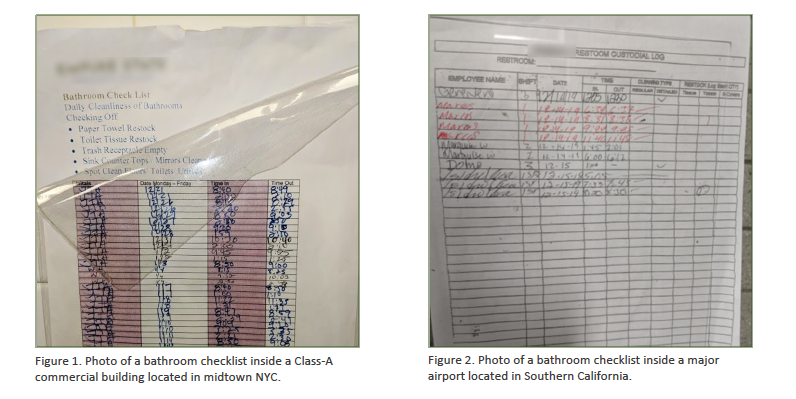
To put things in perspective, there are at least 5.6 million commercial buildings in the U.S., representing over 87 billion square feet of floor space, roof-top and grounds. That square footage is expected to reach upwards of 126 billion by 2050. Just as impressive in scale are the tens of millions of workers that are required to keep these facilities running, representing a total payroll that would go toe-to-toe with the GDP of a moderately sized country. In fact, human capital remains the largest expense in property management – more than utility spending.
This is all to say that the property management industry is a behemoth. This is also to say, as we’ve seen with how some restrooms are managed, there is sizable room to improve how the industry manages tasks and the expensive workforce charged with completing this work – an industry optimization, if it were to occur, that could be worth billions in real dollars in productivity savings.
Here’s another figure to chew on: it’s estimated that 40% of facility manpower time has nothing to do with the actual work of running and maintaining facilities. Think about this the next time you are asked to approve overtime or to hire additional workers. This is not to suggest that workers are being dishonest or purposely being unproductive, although this could account for some of the math. Most of this waste, rather, is a direct byproduct of a manual and analog management process – i.e. the paper checklists or work tickets that are ill-equipped to maximize productivity or to keep workers accountable.
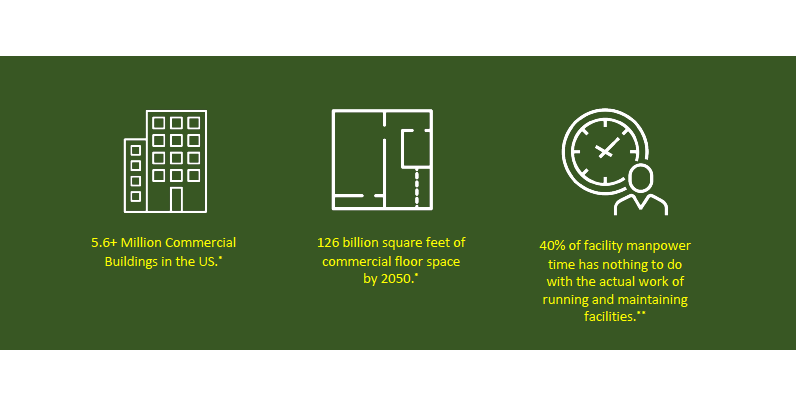
The next time you visit your local pharmacy, you may notice the detail in which pharmacy workers collect data – basically, they scan everything. Some pharmacies now even fit their technicians with wrist bands that are scanned every time they access inventory.
Of course, this strict collection of worker data has its obvious benefits with patient safety. A study found that the use of pharmacy barcode-checking was superior to visual checks in detecting dispensing errors. Beyond patient care, however, this type of data collection can deliver considerable intelligence to the overall operation. How long does it take each technician to fulfill a prescription? How much time are technicians spending on patient consultations? And with machine learning applied to this data, a pharmacy could better predict inventory levels, match staffing with peak customer flow, improve patient care, and so on.
Using the right tools, a similar approach can and should be applied to facilities management. Ultimately, this means first acknowledging that our legacy way of doing things – checklists and work tickets – are ineffective methods of mandating workflows on workers, and just as ineffective at ensuring tasks are done entirely, efficiently, and at a quality baseline.
We must also acknowledge that effectively measuring productivity requires the “fine grain” capturing of information, as well as ensuring tasks are well documented and standardized (and backed by step-by-step guides so that tasks are completed consistently regardless of who’s performing the work). This is also the only way machine learning algorithms can be applied to uncover task prioritizations, service delivery failures, and frequency of requirements.
With this in mind, let’s revisit our troubled bathrooms from earlier and look at how worker and task data should be collected and what type of intelligence we may be able to get out of it.
Instead of a paper checklist taped to the wall, what if the janitorial staff at the commercial building I visited were equipped with a mobile workflow tool that required them to follow specific steps each time they inspected the bathroom? And what if we also required them to validate that all steps were completed?
You would achieve the following:
Because the workflow would provide details on each step (with instructions) you would not need much, if any, training for a worker to know what to inspect or how to address issues found in that given bathroom. If a step in the workflow required that each soap dispenser was quickly photographed and/or scanned to verify product levels, you would never encounter an issue where a worker would forget or neglect to check the soap… And they know you’ll know.
With automatic timestamps from the mobile app, you would get an accurate measure of how long each bathroom inspection took to complete. You would get a clear picture, over time, of which workers completed the task most efficiently, and, just as importantly, which workers were not being efficient. To take this even further with machine learning intelligence, you could better predict the frequency and optimal times bathroom inspections were needed (if you cut out unnecessary inspections, for example, that’s real productivity saved). You would also be able to schedule staff where they are most optimal. In the fleet management world, they call this Route Optimization.
With this simple example, we can clearly see how smart, digitized workflows and the details they capture could not only improve (and ensure) the quality of work that is performed, but also how that collected data could be leveraged to optimize where manpower is being spent. Now imagine applying this tool across all aspects of the operation.
Having well-documented and digitized workflows may address another fast-approaching issue. And this is a hard truth to accept: the facilities management industry has an aging population problem. It’s estimated that 40% of the labor force will retire over the next seven years. That’s a lot of institutionalized knowledge walking out the door in a relatively short amount of time. These are the workers with intimate knowledge of how things work in your facilities, much of which are nuances and unique details that are probably not documented anywhere.
Combine this problem with our all-time-low unemployment levels and labor shortage, and we find ourselves in an environment that will require enterprises to rethink their methods in order to remain competitive – all without losing sight of maintaining quality service. As a result, the industry will be forced to document and digitize all processes and workflows; they will be required to be hyper-vigilant about productivity and efficiencies. Managers will need to attack the situation differently, not by just throwing more bodies at it.
In other words, in order to survive, facility managers will need to work smarter, not harder.
At StringBean Technologies, which aims to make facilities management more intelligent with digitized workflows, we have been working closely with clients to uncover data they had never tapped into before. We’re showing them what activities take more time and where it varies by and between staff for training and monitoring purposes.
We are also equipping our clients with the ability to build in rules in their workflows to catch anomalies and errors. For example, water meter readings should never be lower than the previous record (which we show occurs in Class-A buildings 8-12% of the time). We also flag standard deviations of tasks. So when items fall below or beyond tolerance levels, alerts automatically indicate and escalate a problem, an abuse of time management, or service quality failure.
The chief engineers and senior facility management we serve welcome this data; they can finally validate how their manpower spends their time, authenticate and validate why they need more resources, create incentives for efficiency and performance; and allow technology to track, guide and measure it. They are also beginning to see the broader value of integrating this powerful data with other data, making their operations even more efficient and predictive.
With much of your labor pool leaving the workforce in the next seven years, it will be more important than ever that your organization also takes steps to begin digitizing your workflows and learn from your productivity data.
This is the last bastion of low hanging fruit that facility managers and owners can quickly tackle to save time, money and lead the future of innovation in PropTech.
About the Author
Reuben Levine is co-founder and managing partner of StringBean Technologies. Previously, Reuben worked as a senior banking and finance executive before becoming an entrepreneur eighteen years ago. With expertise in process engineering, Reuben spent over two decades launching and revitalizing people, process and paper-intensive business systems, both on the buy-side of large enterprises and sell-side early-stage technology innovations. Reuben led the consolidation and insourcing of multimillion-dollar customer service and help-desk operations for Chase Manhattan Bank, IBM, Hewlett-Packard and Fuji. Reuben most recently owned and managed one of the northeast’s premier fire and environmental trade services companies, designing and delivering large-scale facility management solutions to the property management community throughout the Tri-State area. In an effort to re-tool this enterprise’s technology, Reuben helped seed and commercialize FieldOne Systems, which was purchased by Microsoft in July 2015.
Connect with Reuben on LinkedIn.